SHARPENING CHISELS
Greater hardness means that the edge is more brittle in carbon steel
Japanese chisels are made by forge-welding a layer of carbon steel to a softer iron backing. After shaping, hardening and tempering, the carbon steel forms the cutting edge and the iron adds toughness to withstand the impact of a hammer.
In addition, sharpening is made easier because only a part of the bevel surface is the harder metal. In order to bring the steel to the degree of hardness that can be sharpened to such an excellent edge, the tempering temperature, following hardening, is lower than that used for most other such tools. To avoid damage in shipping, therefore, the chisel may not have received the final steps of sharpening by the maker.
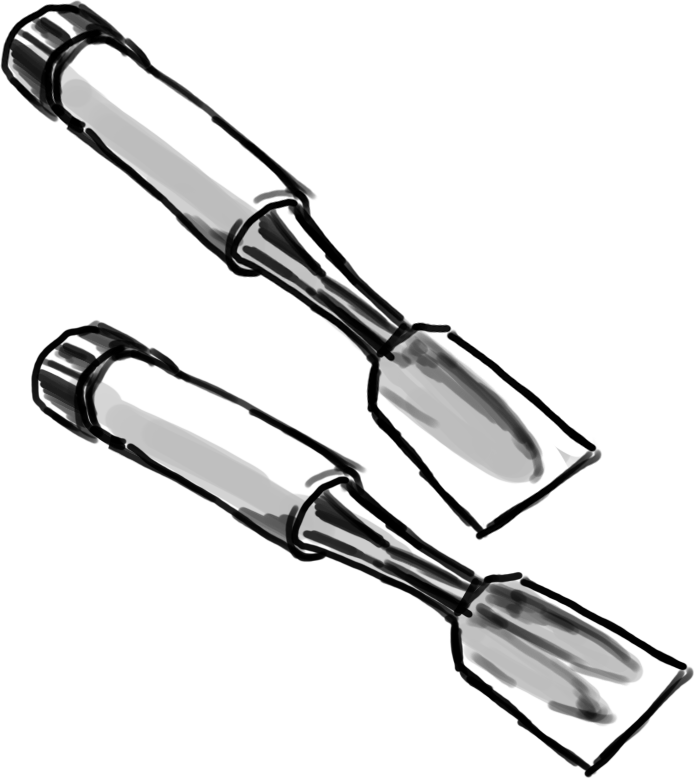
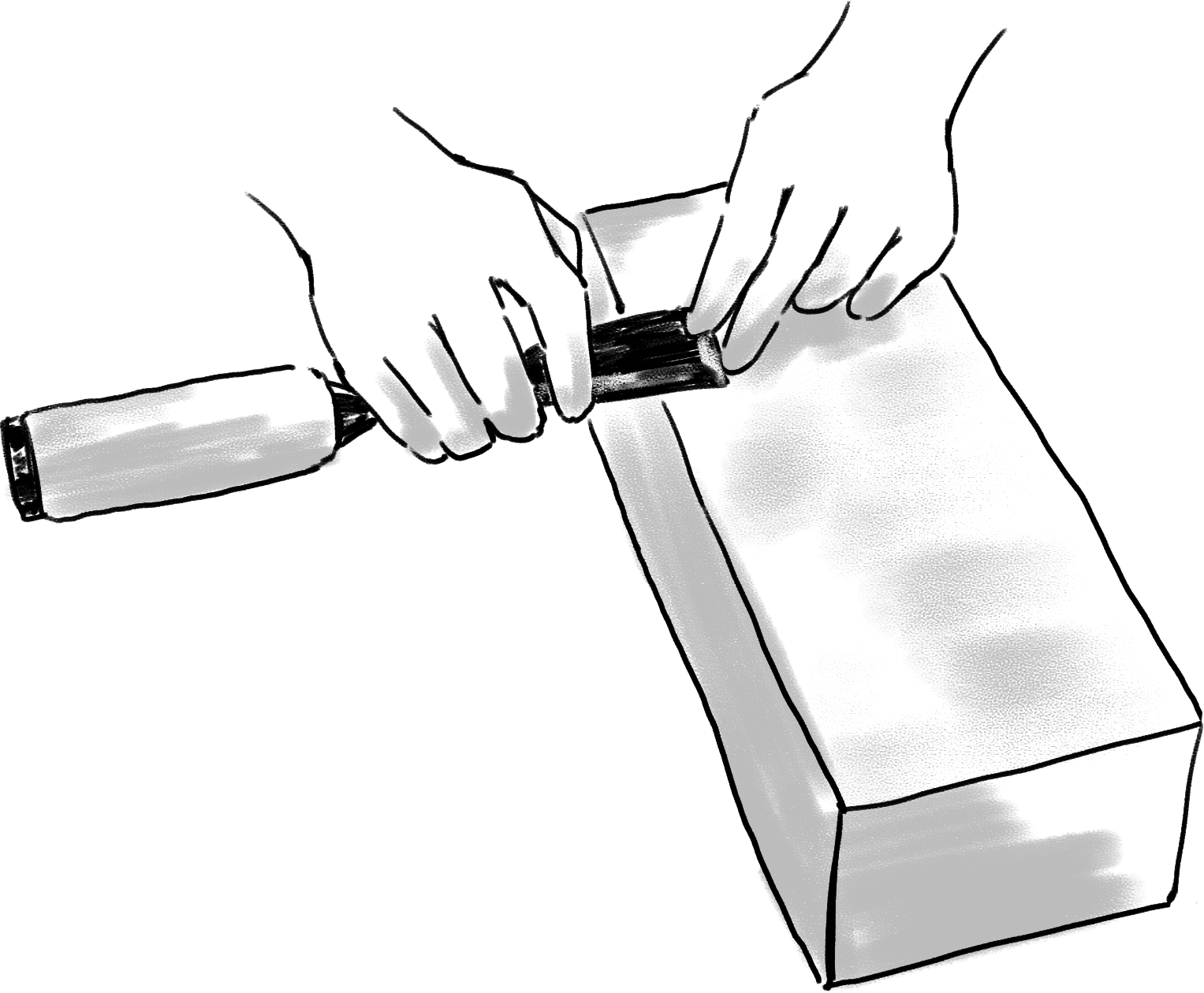
Notes on sharpening
To prepare these chisels for use, the bevel should be honed first on a waterstone of 800 to 1000 grit. Never use a dry grinder, because the heat produced will soften the cutting edge, just as though it had been tempered to a higher temperature.
This damage to the blade will occur before the appearance of the blue color that is often considered an indication that the edge has been softened excessively. The initial refinement of the edge should be followed by additional honing of the bevel and back, alternately, on finer stones. If the chisel is then maintained properly, the flat back should require only slight honing on the finest stone to remove the wire-edge that develops as the bevel is honed.
Never break the wire-edge off, because that will leave the cutting edge rough and unable to reach the peak of its capability. Use a coarser stone only when repeated sharpening of the bevel has removed the narrow fiat at the cutting edge of the back.
avoid hollow-grinding
It is also important to avoid hollow-grinding, even with a wet wheel. That reduces the thickness of metal behind the cutting edge, leaving it more vulnerable to damage, particularly in hardwood. If a power sharpener must be used, it should be one that uses the flat side of a water-cooled wheel, the bevel angle should be determined. by the type of chisel and the intended use, according to the chart below.
RECOMMENDED BEVEL ANGLES
Finish chisels 22-30 degrees
Mortise chisels 25-30
Slick chisels 22-28
Timber chisels 24-30
The higher angles within each range will provide a more durable edge for use on harder woods. To further reduce the possibility of damage in such operations as mortising, be sure to use the chisel to cut each chip-free; do not use it as a pry bar to break off a partially cut chip.
The higher angles within each range will provide a more durable edge for use on harder woods. To further reduce the possibility of damage in such operations as mortising, be sure to use the chisel to cut each chip-free; do not use it as a pry bar to break off a partially cut chip.
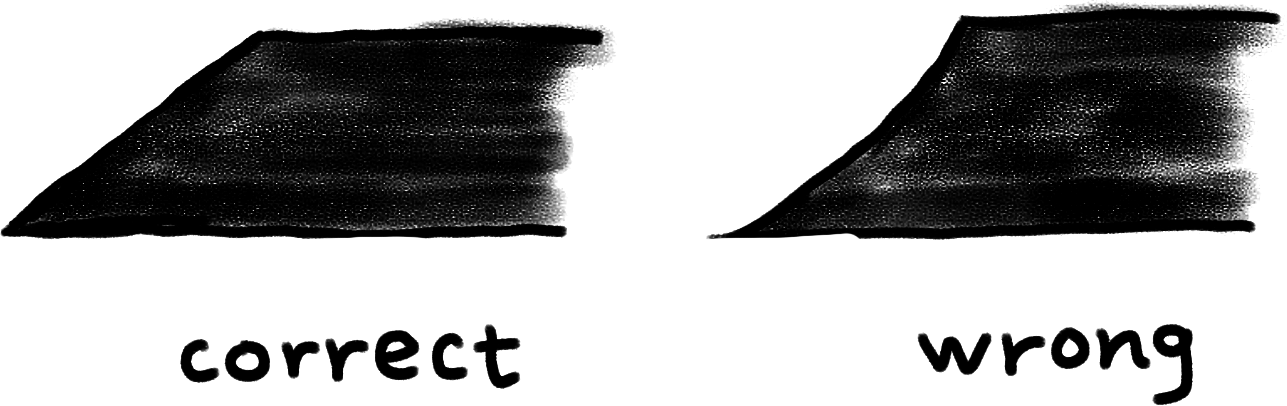